Building Silver Origin while Overcoming an Act of God
The construction of Silversea Cruises’ new Silver Origin, the 100-passenger expedition ship that will sail in the Galapagos Islands, is now complete. The story of its construction, with many of its final stages occurring in the midst of a global pandemic, is quite an unusual tale, a display of resilience, determination and fine European craftsmanship from Dutch shipyard De Hoop.

This feature, written by Fre Drenth, the Director of De Hoop Shipyard in the Netherlands, offers fascinating insights into not only the process of building a new expedition vessel but also into how the challenges of a global lockdown, with the need for ever more rigid safety procedures, a reduced workforce, and the necessity to create ingenuous solutions to overcome challenges became a daily occurrence.
On January 16th, the building of Silver Origin was well underway. The photo below shows the aluminum sunroof being placed for fitting purposes. On the right-hand side is the accommodation barge, Rossini, built by us in 2012—at that moment with 200 sub-contractors on board. Construction progressed well until March when the global situation changed.
At the beginning of March, the coronavirus slowly entered Holland and the Dutch lockdown commenced on a Sunday afternoon, March 15. All public facilities closed and people were advised to stay at home as much as possible. Over the following months, the global lockdown posed more challenges to the construction of Silver Origin than we could have anticipated.
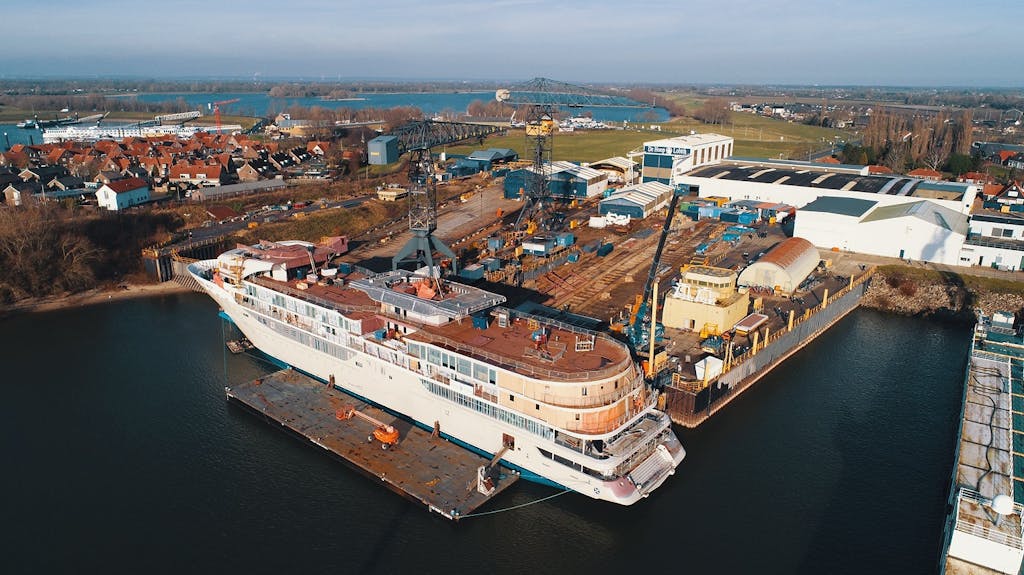
Strict Sanitary Measures
The Dutch health organization, RIVM, issued guidelines on how to operate, which we followed closely, as well as the advisories set out by the World Health Organization. Because our workers were living and working in such close quarters, we also quickly implement the following COVID-19 procedures at the yard, which were developed in close cooperation with Royal Caribbean Cruise Line and all contractors. We evaluated these measures on a daily basis to protect the safety of all.
- Internal Communications: We distributed internal communications to our employees on our new protocols, reducing contact between colleagues and adapting our working methods. Our key messages were:
- If you are showing any symptoms, stay home and inform the company immediately.
- If you are considered at-risk due to underlying health conditions or if you do not feel comfortable to continue working, you are encouraged to stay at home.
- Daily Health Checks: We monitored the health of our entire team, checking for symptoms daily. On top of our preventative measures, we took the temperatures of our staff every day—sometimes twice per day. We stuck colored stickers to the helmets of all who were clear.
- Space Restrictions: All workers had to remain more than 1.5m from each other at all times, to respect social distancing rules. We minimized the number people within the restricted areas and reduced workers’ contact circles with fewer meetings.
- One-Way System: Throughout the corridors of the ship, we implemented a one-way walking system.
- In the Canteens: Our staff canteens were set-up in line with the preventative requirements, including enhanced cleaning measures, distancing between diners, and even stricter food safety protocol.
- On-Site Accommodation Facilities: As workers were living in on-site accommodation – barge Rossini – we had to ensure that they were protected. We reduced the capacity from 200 to just 100, with one person sleeping in each cabin instead of two.
- Sanitary Protocol: Our cleaning teams worked extra hard to clean more thoroughly and more regularly. We also provided our workers with extra facilities for washing their hands.
We also established an emergency quarantine plan to prepare for the unlikely scenario of large-scale contamination, which would of course have meant the closure of the site.
Fortunately, the works were performed in relatively isolated areas, which reduces the risk. The first major challenge we encountered, however, was maintaining our workforce.
Maintaining a Team
De Hoop Shipyard employs 140 people, plus an additional flexible workforce of just over 100 people. At the busiest period, we were putting the skills of approximately 250 professionals to use on Silver Origin. When the lockdown came into force, we left everybody free to choose whether they continued to work or whether they returned home. Many foreign workers left the yard to reach home before the borders of their respective countries closed. We therefore had to source new workers, which proved to be very difficult during a global pandemic, but we succeeded in finding new staff and maintaining a workforce of roughly 200. The lodging capacity on Rossini was reduced from 200 to 100 people.
We tried to continue with our work as normal. However, due to the absence of a few individuals, who had to perform duties at home, such as childminding in the wake of school closures, we proceeded at a somewhat reduced pace.
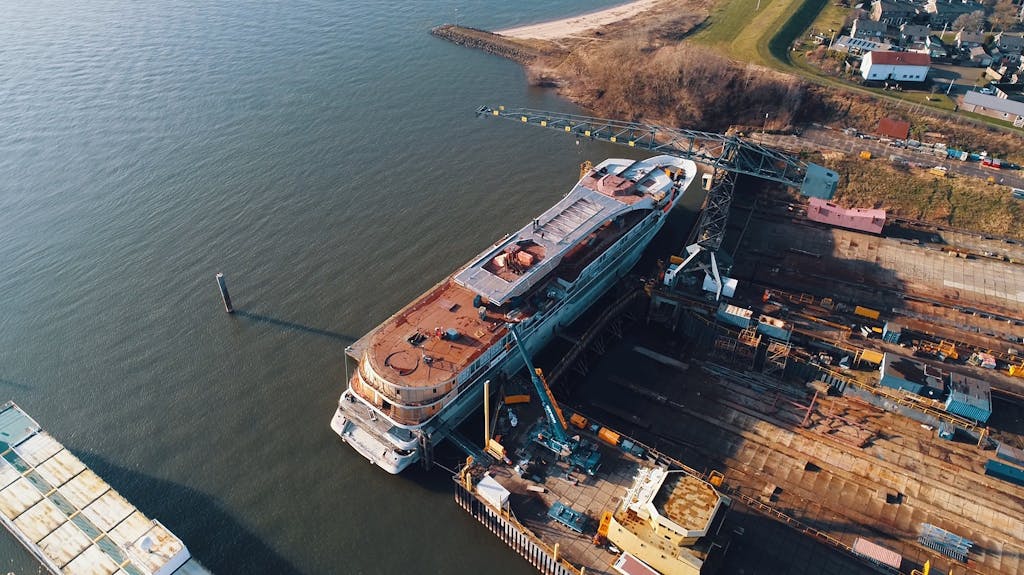
Italy entered into a national lockdown on March 10, which proved to be problematic: two of our main subcontractors, Oxin and Somec, are based in Italy, and so work on the ship’s windows and Galley was disrupted. We simply couldn’t get the materials we needed. Eventually, we managed to source these parts and the project came together.
On the vessel, the teams kept working, kept distancing from each other, and the one-way traffic system on board worked well. Communications between stakeholders were mainly conducted through virtual meetings online, which was more time-consuming but ensured safety. While the working weeks were long, the morale and team spirit were both very high.
The location of De Hoop Shipyard is relatively isolated from the rest of Holland, and a large percentage of our workforce lived on the yard, or close by. People continued with their jobs, ensuring safety at all times, and were not deterred by the coronavirus. I was very proud of the team.
Repositioning Silver Origin to Rotterdam

While shallow waters on the Waal River delayed Silver Origin’s float from November to December 30, 2019, the months of January and February brought lots of rain to Western Europe in 2020, leading to long periods of high water. This kept Silver Origin locked behind 12 bridges leading to the sea from De Hoop. Only on March 26 was a safe passage to Rotterdam possible — over one month later than originally planned. This left only four weeks between arrival in Rotterdam and the sea trial date. We still had a great deal to prepare, so time was against us.

Once the water levels dropped and we were finally able to reach Rotterdam, we encountered more problems during the commissioning phase. Because the international borders had closed it became more difficult to get the right engineers on board to start up the systems. We were not only missing supplies, but we were also in short supply of expertise for certain tasks.
Replacing damaged components became almost impossible and it was difficult to get certain supplies delivered on time because delivery services were affected. We were still missing the ship’s carpets, most loose furniture items from Italy, and all artwork — I guess artwork is particularly tough to ship during a global pandemic!
Fortunately, as most equipment on board was Dutch, we were able to improvise, but simple things like electrically adjusting sliding fire doors became a big hurdle that cost us time. And we were already battling against the clock. Nevertheless, the ship looked magnificent in time for the sea trial and we were all eager to put her through her paces on the open water.
An Innovative Sea Trial
We were well prepared for the ship’s sea trial—to be held off the coast of Goeree-Overflakkee, close to Rotterdam Port—but circumstances were far from normal and this was to be no ordinary test. We came up against a potentially project-halting challenge: Navis, a St. Petersburg-based company who produced the computer software for Silver Origin‘s propulsion and steering installation, could not reach the ship. Navis’ engineers were required for the commission and tuning of the software, which is a time consuming job and can take between 4 and 8 hours. Nevertheless, we managed to devise a solution, which, to my knowledge, had never been tested during a sea trial and would push the boundaries of engineering.

It was decided that Navis would tune the ship’s dynamic positioning system remotely from the company’s office in St. Petersburg, Russia—over 1,800km away. We established a fast internet connection on the vessel to enable fast communication with minimal time delay. The communication was tested before the sea trial and all went well. Using just a headset and a built-in camera, contact with the vessel was made.
Silver Origin’s dynamic positioning system controls the ship’s bow thrusters and azimuth thrusters. As borders with Finland were closed and a required engineer couldn’t attend the sea trial, a stand-in engineer was appointed to commission the thrusters, working closely with the engineer in St. Petersburg. After testing of the propulsion installation, we gave the vessel to the control of the engineer in St. Petersburg. This went very well, in part due to the fact that this engineer had a great deal of experience.

The engineer successfully conducted all maneuvering tests, while the vessel’s captain acted as his lookout. When the current brought the vessel too far off position, the team in St. Petersburg sailed the vessel back to the starting point. It was a very strange sensation to feel the vessel respond to someone in a distant country.
The tuning was successful and took no longer than normal. Our sea trial demonstrated, for the first time ever, that it is possible to tune dynamic positioning systems remotely. It could save companies time and money in the future.
Thanks to good teamwork and strong expertise, we had the complete dynamic positioning system up and running within one day. The official trials took two days and, thanks to the cooperation of all involved, we entered Rotterdam late on a Wednesday night with all tests successfully completed. The feeling was euphoric.
Looking Ahead
At this moment in time, we are in the final stretch to delivery, working away at all remaining points. Approximately 45 workers remain on board Silver Origin, accommodated in the ship’s guest suites. As a result, all guest accommodation has been tested well before Silversea’s guests will enjoy it in the Galapagos Islands.
The coronavirus has had a dramatic impact on the global cruise industry, but we maintain a positive outlook. The construction of Silver Origin, with its challenges and the solutions we found to overcome them, symbolizes the resilience of European industry. As we understand it, travelers are willing to cruise as soon as they can. This keeps us positive.